The single axis motherboard IONICUBE 1X design is ready and sent to PCB fab for prototyping today. Prototype should be here within 2 weeks.
Category Archives: Ioni
Speechless
The wait is over!
Everything is ready for launch now, so we don’t hesitate to do it! IONI and IONICUBE products can be obtained with very attractive launch campaign prices through INDIEGOGO crowdfunding site and at normal prices through the web shop.
Indiegogo campaign ends in after 21 days and purchases are realized if campaign goal is met during that time. So please share the link and get people involved to make it happen!
Indiegogo campaign
We are going to launch an Indiegogo campaign where one may obtain IONICUBE and IONI Pros for a very attractive prices for a ~20 day period. I would put a countdown timer in here, but I’m not sure if there is some form of acceptance for IGG projects before they appear publicly. Anyway, it shall become online within this week! Same time these will appear on the web shop for immediate purchasing.
Meanwhile, please take a look on the latest video:
Short circuit test
Testing IONI servo motor drive short circuit ruggedness. Drive supplied with maximum voltage and spinning a 1 kW motor maximum speed while it’s being short circuited (it’s the worst case scenario).
Spoiler: it does not break.
Yes!
IONIs arriving this week
Just got message from the PCB assembly house that the first pilot batch of IONI drives are scheduled for delivery late this week. If they do arrive, and everything goes as planned, we might see the first shipments next week!
The drives will appear on the web shop when we are ready for shipments (no pre-orders are taken, but there is probably enough for everyone).
PS. I apologize my absence from the blog lately. I was on travel during the last week and my laptop broke down.
Single axis IONI motherboard
IONI documentation in the works
While we wait the first production batch to arrive, it’s good time to make the documentation. Thankfully IONICUBE makes things so simple that it’s an easy job!
If we succeed with Mach4 plug-in (and perhaps for some other software too), then it becomes even simpler.
Maximizing the bandwidth of Torque Control
The latest achievement in IONI servo drive development was the maximization of torque control bandwidth. IONI actuates motor by a 20 kHz pulse width modulated (PWM) power output which essentially means switching the supply voltage between 0V and supply voltage (HV+) very fast causing the desired current to flow in the motor coils. Drive samples coil currents once at every PWM cycle and also re-calculates the PWM duty cycles on every cycle.
Last couple of we have spent perfecting the torque controller speed without sacrificing the dynamic range or smoothness. Bandwidth of controller is dictated by two factors: update rate and delay. Update rate was already at maximum (every cycle) but previously the delay was one full PWM cycle (50 µs). By optimizing code enough, drive is able to complete torque control calculations within half PWM cycle (<25 µs) which shortens the delay by 25 µs.
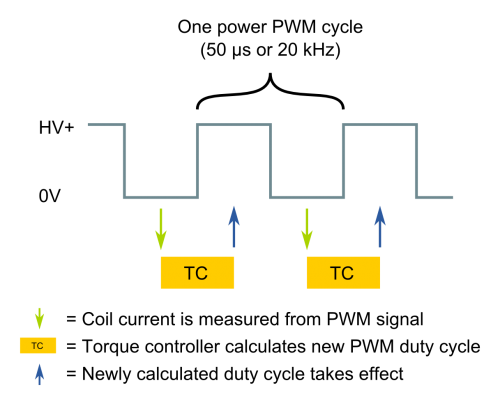
High bandwidth torque control timing diagram demonstrating half PWM cycle delay and full PWM frequency update rate. Torque controller has the highest bandwidth when the update rate is at the maximum and delay at the minimum.
Ok, 25 µs doesn’t sound much. But it actually is more notable than it first seems. This change yields 30-50% boost in torque control bandwidth which can be seen sharper change of torque without causing any overshoot. This allows us to set position and velocity control gains higher without losing stability. In the end, the result is more stable and more stiff servo motor.
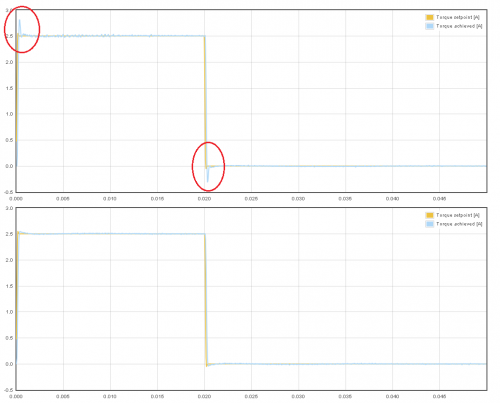
Torque controller step response with one PWM cycle torque control delay (top) and half PWM cycle delay (bot) without changing torque controller gains. Notice the overshoot caused by the additional delay. The overshoot can be cured by lowering torque control gains, but that also reduces bandwidth.
Never seen servo motor so stiff :)