We run number of tests to each manufactured drive, one of them being a load endurance test. The test is done by driving constant 9 Amp sinusoidal current from all four power lanes and clocking the time of how long it takes drive to heat up by 25 Celsius. This test is used to verify proper characteristics of the power stage. Each tested drive must score above a certain level of endurance to be passed.
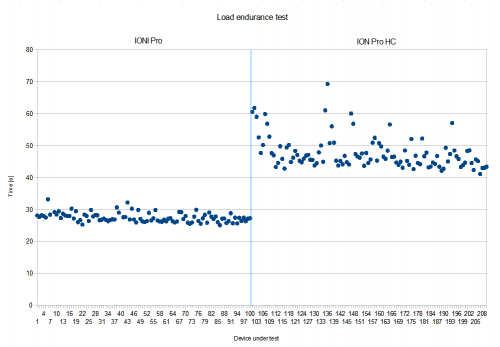
Load endurance test with IONI Pro and IONI Pro HC
The statistics above shows endurance results from about 200 tested drives. From here we can see that Pro HC model has average endurance times of 47.7 seconds while Pro has average of 27.5 seconds. This means that on average HC model takes 1.73 times longer to get equally warm during the test. On the other hand, it could be understood that on average HC model dissipates 42% less heat.
The test also reveals that the variance is higher on HC model. There are few extraordinary good units probably due to varying characteristics of the MOSFETs even though both model MOSFETs are made by same manufacturer. Pro HC model uses the newest and lowest loss type that is available today in this size while Pro uses couple of steps lower rated devices. I hope some day the MOSFET manufacturer manages to avoid the variance and start offering transistors that perform like the best ones seen here.
Despite of the variance, the best thing is that there is clear bottom level on both types, so any unit will not have troubles meeting the specs.