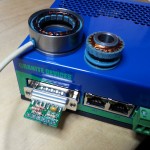
A resolver (stator and rotor part) and an adapter card plugged to Argon
Resolver feedback device will get an official support in the next Argon firmware release. Connecting a resolver to the drive requires few passive components between the feedback device port and actual resolver. These are easily fitted inside the D-sub connector hood and pre-made PCB’s for that will be available for low cost.
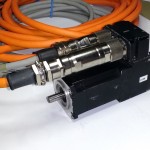
A bit oversized plugs on the motor under test?
The main concern using analog feedback device (in which category resolver belongs) is the sensitivity to electromagnetic interference. The following images illustrate the importance of proper cable shielding when using resolver. The upper image without cable shielding/screening shows significant amount of position sensor noise which would cause motor hissing and hunting while standing still. The lower image shows nearly ideal stability. In both cases motor is standing still in torque mode, so all we see here is not real movement but just the sensor noise.
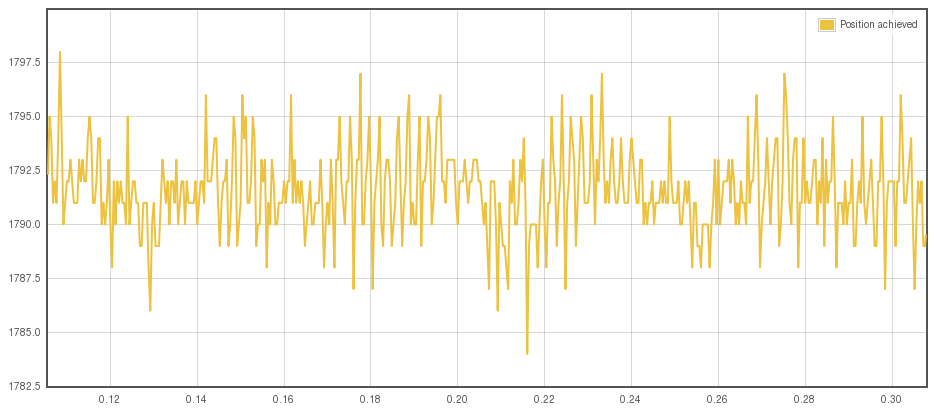
Resolver position counter noise when motor or resolver cable shield is present but not connected to drive. Noise amplitude is over 10 counts out of 8192 per revolution.
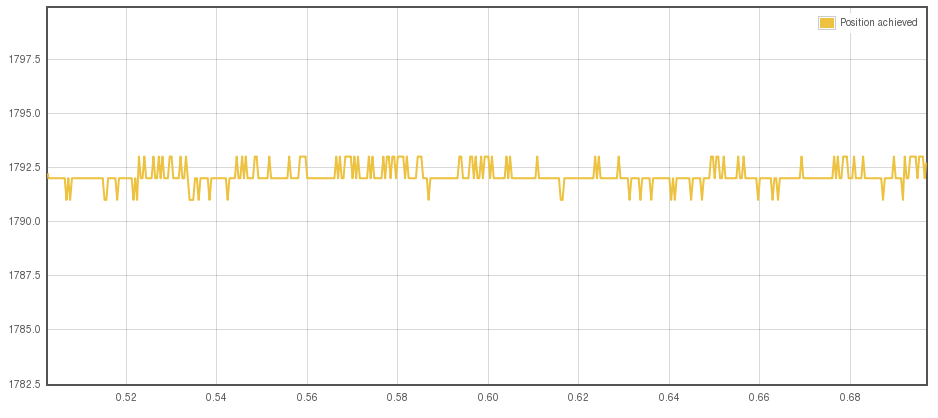
The noise when motor or resolver cable shield is connected at drive end. Noise amplitude has reduced to about 1 to 2 counts out of 8192 per revolution.
Random fact of the day: I typically use the most horrible imaginable wiring when developing & testing drives. This serves two purposes: saves time and reveals potential problems early. If it works reliably with bad wiring, then it damn sure will work with a proper wiring.