Testing procedure of Argon drives is ~80% done now. The testing system consists of:
- Hi-pot tester which verifies insulations at 1.5 kV AC voltage
- Testing hardware (artificial test load, various I/O testers, etc)
- Testing software for the above hardware
- Test functionality in firmware
The testing software is based on Granity with some modifications.
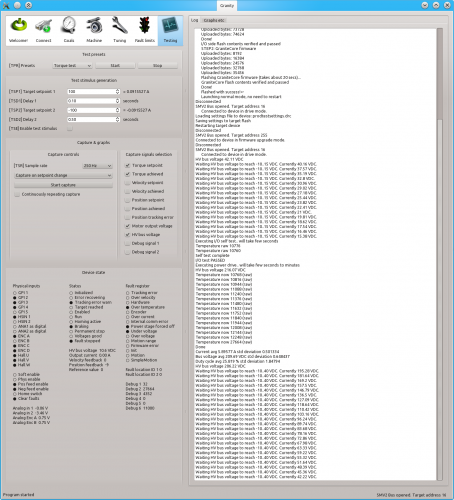
Argon testing application work in progress. Most of the UI stuff will be ripped off from the polished testing version and instead provide only a simple “start test” button to eliminate human error.
I will start testing the first drives as soon as the test software fulfills it’s all technical requirements and bring first drives to market ASAP. Polishing the software for assembly house can wait couple of weeks as it will affect only next production batches.