Motor coil current sensing is one of the most critical component in a well behaving motor drive. This is true because current readout data is being used as feedback signal for closed loop torque controller as motor torque is directly proportional to coil currents. The importance of good torque control can be understood by knowing the fact that the the final step in drive’s signal path is always a torque controller. This means, any error in current sensing will eventually reflect to motor shaft, no matter which control mode is being used.
Today’s big achievement was the implementation of adaptive current sensing for high dynamic range torque control (HDRT) for ION drive. The captures below reveal the inner workings of this technology.
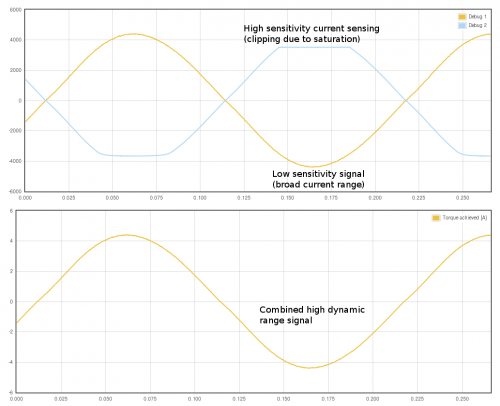
Illustration of measured current signals from ION. Each phase current is measured in two channels: with high sensitivity and low sensitivity. The high sensitivity signal has higher precision but is limited to about +/-3.5A range. The low sensitivity signal has range of +/-23A but comes with less precision. The drive combines these two signals into one by making it both precise and high dynamic range.
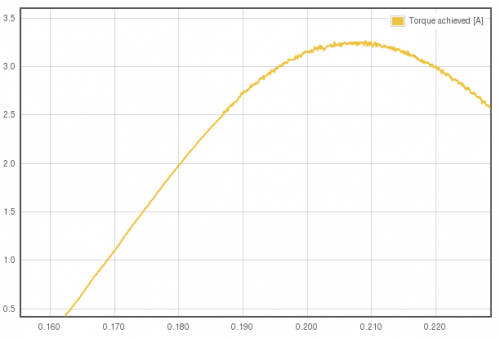
Zoomed image of the combined current sense signal. The switch between high and low sensitivity happens at 2.5A. As seen from the image, the curve above 2.5A is bit more rough than below 2.5A.
One major motivator behind HDRT is to expand the range of motors that can be driven with single drive without exhibiting any of the typical drawbacks that come when a small motor is being driven with a large drive (motor hiss, jitter, torque ripple, position hunting). It also gives maximum precision for those who want the best performance in torque control mode.
Both ION and ARGON utilize low noise 12 bit analog-to-digital converters (ADC) and discrete Op-Amps for acquiring the sensor signals yielding the effective current sense precision of 14 to 15 bits. Most of the drives I’ve examined use a single sensing range and a 10 bit ADC. That is a significant enough difference to be seen, heard and felt by anyone :)