After a long wait, the first batch of final version of Argon servo drive enclosures have arrived! Some minor changes were made to the design and also manufacturing quality has been improved based on our feedback. In the prototype series there were paint burrs in threads and small bending inaccuracy making assembly some times bit challenging. All these are now gone and the outcome seems flawless!
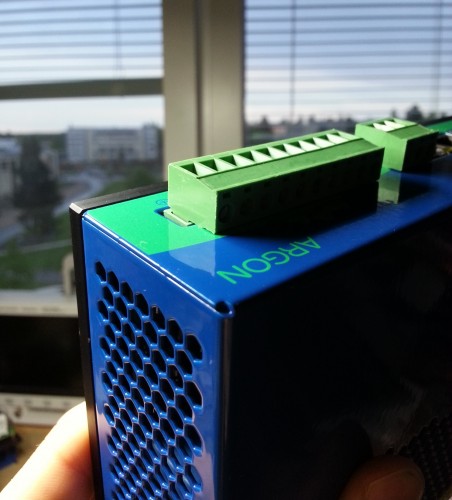
Argon final enclosure corner detail. Notice also hexagon shaped vent holes for minimal air flow resistance.
As Argon may be used for wide power range from 50 W to 1500 W, the cooling requirements will vary. To help high power users, we made mounting holes for standard low cost “half brick” heat sinks.
Tomorrow the enclosures will continue their journey to electronics assembly house where drive assembly will begin in just few days.