Resolver feedback device will get an official support in the next Argon firmware release. Connecting a resolver to the drive requires few passive components between the feedback device port and actual resolver. These are easily fitted inside the D-sub connector hood and pre-made PCB’s for that will be available for low cost.
The main concern using analog feedback device (in which category resolver belongs) is the sensitivity to electromagnetic interference. The following images illustrate the importance of proper cable shielding when using resolver. The upper image without cable shielding/screening shows significant amount of position sensor noise which would cause motor hissing and hunting while standing still. The lower image shows nearly ideal stability. In both cases motor is standing still in torque mode, so all we see here is not real movement but just the sensor noise.
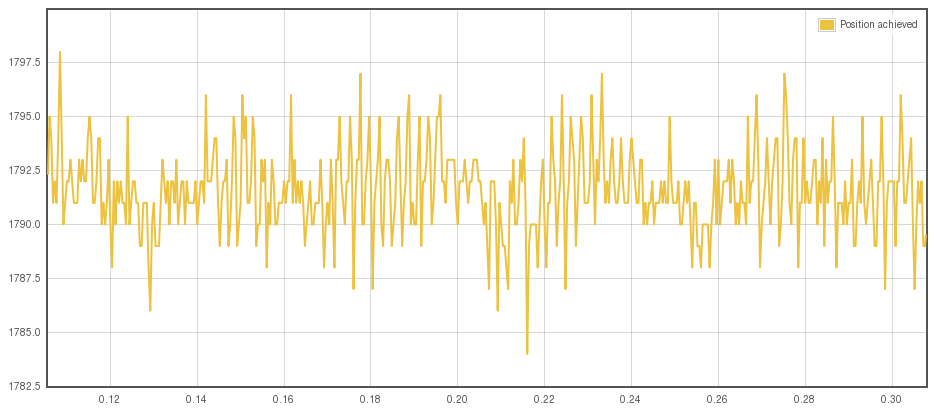
Resolver position counter noise when motor or resolver cable shield is present but not connected to drive. Noise amplitude is over 10 counts out of 8192 per revolution.
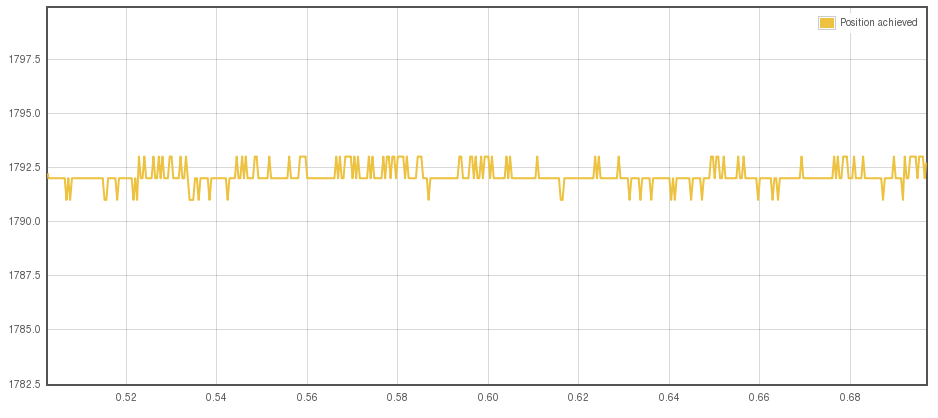
The noise when motor or resolver cable shield is connected at drive end. Noise amplitude has reduced to about 1 to 2 counts out of 8192 per revolution.
Random fact of the day: I typically use the most horrible imaginable wiring when developing & testing drives. This serves two purposes: saves time and reveals potential problems early. If it works reliably with bad wiring, then it damn sure will work with a proper wiring.
hi Tero
when are you planning to release the firmware that will read linear scale Cos Sin?
I need for my project to the axis control by linear scale Heidenhain LS403
Yes, SinCos support is the next addition right after resolver support is there. Do you use also linear motor in this system or rotary with lead screw?
Hi
I use rotary motor (DC) with lead screw and linear scale
there are no rotary encoder in my system (for now)
That calls for dual loop feedback system. Linear encoder only usually leads to stability problems if there is any backlash or flexibility between the rotary motor and linear motion.
Dual loop system means that there is feedback device on motor that is used in conjunction with the linear encoder.
BTW, Argon hardware has been designed for dual loop, that only needs to be done in FW side too. I’m still thinking how to make it clean and transparent way.
I do not want to put a dual feedback loop on my machine, I shod possibly a trial as an experiment, just for the challenge
but I’m looking forward to the FW Update argonto be able to use the linear scale COS / SIN
If you’re lucky, machine is very rigid and servo stiffness requirements are not the most extreme, then it may work. SinCos encoder can be used with Argon already, the only missing thing is the analog interpolation of signals. So you will get only digital interpretation of encoder signals until the FW upgrade is ready.
I assume that the adapter card will fit into the FCI housing that is pictured in the wiki?
http://granitedevices.com/w/images/d/d6/Argon_test_stup_closeup_m.jpg
Haven’t tested but highly likely that it will fit in it as well as 90%+ to all other housings.