New Argon servo drive firmware is under preparations. One of the improvements will affect to performance at high electrical commutation frequencies. High frequencies occur at high rotation speeds especially if motor magnetic pole count is high (more than 4).
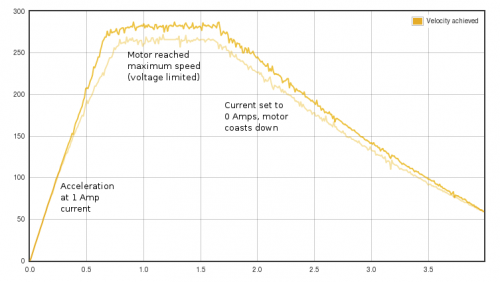
Performance change illustrated. In this test motor was accelerated with constant 1 Amp current in torque mode before (the light yellow graph) and after FW upgrade (dark yellow). From the graph we can see how the new FW accelerates motor faster and reaches higher speeds meaning it delivers more torque at high speed region. The motor is a 300W Sanyo Denki P5.
Before releasing it, we’re planning to implement also configurable motor braking control that will help people with vertical axes where gravity tends to pull unpowered axis down.
hi Tero
a question about the future possibility of argon
I have a machine configuration that allow myself to have two encoder feedback for axis
1 linear encoder 1 and rotary encoder
it can be used to eliminate the problems of backlash in the endless screw
in a future firmware would it be possible to have encoder feedback COS / SIN and return TTL simultaneously?
thank you
Dual-loop feedback support is in the plans and designed in the hardware already. However there are many FW things to do before it.
Do you mean TTL encoder output? No encoder outputs are in the hardware.
no I’m not talking about TTL output from argon for feedback value encoder
I would compose my dual loop encoder feedback with 1 TTL (quadrature) and 1 SIN / COS encoder (1 Vp-p)
it’s possible?
It should be possible to connect SinCos and digital encoder to J1 connector simultanously (at least it’s designed to allow that), not yet tested though.
Second way would be to put digital encoder to J5 connector but that would replace step/dir input that many people need.
Good to hear, you are planing to do dual-loop feedback in Argon. I found this feature in Dynomotion Kflop controller but don’t know much about it.
I can only imagine that it can be used in taping and drilling application only when x, y axis position are corrected at outer loop then z move down.
Can it be used in 3d milling also?
Dual-loop feedback allows one to use two feedback device on single axis. It won’t enable new possibilities but enhances system accuracy because lead screw backlash, pitch error and flex can be automatically compensated on the fly.
Typically with dual loop feedback, the encoders are used for different purposes, such as:
–rotary encoder is used for velocity feedback
–linear encoder is used for position feedback
I’ve used a dual loop setup twice, one with a MEI board and once with a Galil 18xx (that was a fun system, it had air bearings, flexures, and a granite table).
It is correct that only velocity information is required from the inner loop. Without it any backlash or flex of the mechanics would render system unstable – or very allow only very sluggish tuning.